Come i progressi nelle plastiche alternative potrebbero aiutare ad affrontare la crisi dei rifiuti / How advances in alternative plastics could help address the waste crisis
Come i progressi nelle plastiche alternative potrebbero aiutare ad affrontare la crisi dei rifiuti / How advances in alternative plastics could help address the waste crisis
Segnalato dal Dott. Giuseppe Cotellessa / Reported by Dr. Giuseppe Cotellessa
I progressi nello sviluppo di biopolimeri e plastiche alternative potrebbero aiutare a risolvere il problema delle montagne di rifiuti plastici prodotti ogni anno. Andrew Wade riferisce.
Le materie plastiche, come i cugini idrocarburici da cui derivano, sono intrinsecamente utili. Economiche, abbondanti e multifunzionali, toccano praticamente ogni aspetto della vita quotidiana, dall'abbigliamento, all'imballaggio ed ai beni di consumo, all'elettronica, ai componenti per auto ed ai dispositivi medici.
Ma questa utilità ha alimentato l'ubiquità ed, in assenza di adeguate pratiche circolari, i rifiuti di plastica sono diventati un grave pericolo per l'ambiente. Ogni anno vengono generati circa 450 milioni di tonnellate di rifiuti di plastica a livello globale, di cui meno del 10 percento riciclato. Il resto viene incenerito, inviato in discarica o gettato nei rifiuti, con una stima di 2 milioni di tonnellate che finiscono nei nostri oceani.
In questa fase il problema è ben noto ma, proprio come per i combustibili fossili, il comportamento è stato resistente al cambiamento. A dicembre 2024, i rappresentanti di quasi 200 paesi si sono riuniti per i colloqui INC-5 con l'obiettivo di stabilire un trattato globale sulla plastica. Tuttavia, proprio come per i colloqui COP per affrontare le emissioni, i principali paesi produttori di petrolio hanno bloccato progressi significativi.
Una delle principali sfide con i nuovi materiali come le bioplastiche in generale è che non si integrano facilmente con i flussi di riciclaggio esistenti
Dottor Marc Rodriguez Garcia, Xampla
In assenza di un accordo globale, la migliore speranza per affrontare la crisi della plastica potrebbe risiedere nella tecnologia, modificando la plastica per renderla biodegradabile o sostituendo le materie prime petrolchimiche con materiale vegetale. E con un mercato globale della plastica a nord di 700 miliardi di dollari, destinato a superare i 1 trilione di dollari entro il 2033, l'incentivo è finanziario tanto quanto ambientale.
Una delle sfide più grandi è la plastica monouso, diffusa in tutto, dagli imballaggi e FMCG (beni di largo consumo) alle scatole da asporto ed alle tazze da caffè. Mentre molti articoli monouso, ad esempio le cannucce di plastica, possono essere facilmente identificati e sostituiti con alternative più ecologiche, altri sono meno visibili e hanno funzionalità che i biomateriali faticano ad eguagliare.
"Penso che una delle principali sfide con i nuovi materiali come le bioplastiche in generale sia che non si integrano facilmente con i flussi di riciclaggio esistenti", ha detto a The Engineer il dott. Marc Rodriguez Garcia, co-fondatore e CTO di Xampla .
Nata dalla Cambridge University, Xampla converte materie prime proteiche da piante come piselli, patate e colza in materiali biopolimerici sostenibili. Inizialmente mirata a sostituire una gamma di plastiche monouso, più di recente l'azienda ha ristretto il suo focus.
"La maggior parte dei nostri progressi è stata in realtà concentrata su determinate applicazioni in cui, essenzialmente, i nostri materiali possono sostituire i tipi di plastica che sono impossibili da riciclare", ha affermato Rodriguez Garcia.
Un obiettivo primario per Xampla sono i sottili rivestimenti in plastica applicati a cartone e carta che fungono da barriera contro grasso o liquidi. Questi strati super sottili di polimeri, a volte contenenti PFAS o "sostanze chimiche eterne", sono prevalenti nelle tazze da caffè e nelle scatole da asporto. I rivestimenti possono essere particolarmente dannosi poiché i consumatori spesso credono che l'imballaggio sia riciclabile, quando in realtà gli strati di plastica contaminano i flussi di riciclaggio.
"I rivestimenti sulla carta, ad esempio, sono strati di plastica molto sottili che sono troppo piccoli per essere catturati nei flussi di rifiuti riciclabili esistenti, soprattutto se fanno parte di un materiale separato come una scatola di cartone", ha affermato Rodriguez Garcia.
"La carta può potenzialmente essere riciclata, ma uno strato di plastica molto sottile, che è spesso solo pochi micron... è molto sottile per essere effettivamente catturato nel flusso di riciclaggio... la probabilità più alta è che finisca per essere incenerito od effettivamente disperso nell'ambiente. Quindi tutte le nostre applicazioni sono specificamente focalizzate sul tentativo di sostituire quelle plastiche invisibili e penso che ora sia diventato il nostro USP".
Il rivestimento Morro di Xampla offre funzionalità simili a questi rivestimenti in plastica esistenti, ma consente di riciclare la carta od il cartone sottostante. Un accordo dell'anno scorso con l'azienda finlandese di imballaggi per i consumatori Huhtamäki ed il gruppo di aziende 2M vedrà le scatole da asporto con Morro distribuite commercialmente. Ciò segue un accordo di licenza tra Xampla e 2M affinché quest'ultima produca Morro su scala industriale.
"Produrre questi materiali su larga scala richiede molti investimenti e fondamentalmente molta competenza", ha affermato Rodriguez Garcia. "Ecco perché abbiamo deciso di seguire la strada delle licenze e di queste partnership con aziende come 2M che producono sostanze chimiche e altri ingredienti di origine biologica da decenni".
Un altro caso d'uso emergente per la tecnologia di Xampla è la microincapsulazione, che utilizza il biopolimero per racchiudere cose come oli profumati o vitamine in liquidi. Spesso utilizzata nei cosmetici o nei prodotti per la cura della persona, la microincapsulazione protegge gli ingredienti e può estendere la durata di conservazione, ma si basa su microplastiche dannose per farlo. La tecnologia di Xampla offre un'alternativa biodegradabile.
"Ci sono decine di migliaia di tonnellate di queste microplastiche aggiunte intenzionalmente che fuoriescono direttamente nell'ambiente", ha affermato Rodriguez Garcia. "Possiamo fornire un'alternativa polimerica completamente naturale ad un materiale plastico esistente che viene utilizzato in tale applicazione".
Queste applicazioni "invisibili" monouso prese di mira da Xampla sono frutti relativamente facili da cogliere, dove i biopolimeri potrebbero avere un effetto trasformativo. Ma non è solo il segmento dei consumatori a guidare il cambiamento. La versatilità delle materie plastiche significa che svolgono un ruolo in quasi tutti i settori dell'ingegneria, dove la durata è spesso fondamentale.
Floreon, un'altra spin-out universitaria del Regno Unito, è specializzata in bioplastiche ad alte prestazioni. Basata sulla ricerca nata presso l'Università di Sheffield, l'azienda prende materie prime di biopolimeri di origine vegetale e le potenzia per una gamma di applicazioni, tra cui giocattoli ed elettronica.
"Utilizziamo il PLA (acido polilattico), un polimero ecologico ricavato dalle piante", ha spiegato al quotidiano The Engineer il dott. Andrew Gill, direttore tecnico di Floreon .
"Rendiamo possibile portarlo in applicazioni durevoli, applicazioni che hanno un valore più elevato ed una durata di servizio più lunga. Acquistiamo il PLA pronto all'uso da un fornitore ed il nostro brevetto riguarda la miscelazione del PLA nel modo giusto con cose che gli conferiscono le proprietà di una plastica ingegneristica".
Il PLA su cui fa affidamento Floreon deriva in gran parte da canna da zucchero e mais. Ciò solleva interrogativi sulla sostenibilità delle bioplastiche, con materie prime che potenzialmente sostituiscono le scorte alimentari. Ma secondo Gill, le bioplastiche hanno un impatto trascurabile sull'uso del suolo.
"Per produrre tutte le bioplastiche del mondo oggi, penso che ci serva meno di 1/25 dell'1 percento dell'area agricola globale", ha detto. "Quindi non stiamo competendo con la produzione alimentare".
Floreon ha sviluppato tre prodotti principali a base di PLA. Bio-Tech è un biopolimero sicuro per gli alimenti e compostabile industrialmente, nonché il più ecologico dei tre. A seguire c'è Dura-Tech, una bioplastica più resistente con maggiore resistenza all'impatto, riciclabile ma non compostabile. Infine, arriva l'ultimo sviluppo di Floreon, Therma-Tech, un materiale certificato ignifugo per consentire l'uso di bioplastiche in una serie di applicazioni in cui erano state precedentemente escluse.
"Tutti i nostri gradi hanno molti vantaggi in comune", ha affermato Gill. "Hanno tutti un alto contenuto di rinnovabili. Hanno un basso impatto di carbonio nella produzione e, grazie alle basse temperature di produzione, i nostri clienti possono ridurre le loro emissioni di Scope Two (l'uso di energia nella produzione) e le loro emissioni di Scope Three in base all'impatto di carbonio dei materiali nei prodotti".
In particolare, Therma-Tech ha attirato l'attenzione ultimamente, aiutando Floreon a vincere l'Innovation Award all'evento clou del 2024 della Plastics Industry Association. Primo nel suo genere, il biopolimero ignifugo privo di alogeni sta aprendo le porte all'azienda, portando le bioplastiche in applicazioni che in precedenza erano off-limits.
Per produrre tutte le bioplastiche del mondo oggi abbiamo bisogno di meno di 1/25 dell'1% della superficie agricola globale
Dott. Andrew Gill - Floreon
"È un'innovazione davvero eccezionale in quanto non stiamo solo competendo con le bioplastiche, ma siamo in grado di sostituire le plastiche ingegneristiche ignifughe come l'ABS ignifugo (acrilonitrile butadiene stirene)", ha affermato Gill. "Plastiche ignifughe: ci sono molte preoccupazioni circa l'impatto sulla salute e sull'ambiente dei ritardanti di fiamma alogenati che vengono utilizzati oggi in quelle applicazioni".
A causa del potenziale rischio di cortocircuiti, le materie plastiche utilizzate nei dispositivi elettronici devono avere un certo livello di resistenza al fuoco. La classificazione specifica che i clienti di Floreon stavano cercando era UL 94 V-0, uno standard di settore in cui un campione verticale di materiale viene incendiato dal basso, quindi deve autoestinguersi in modo sicuro entro 10 secondi senza gocciolamenti fiammeggianti.
"Quando si ferma, riaccendono la fiamma per altri 10 secondi e fanno lo stesso", ha spiegato Gill. "Far sì che un materiale di origine vegetale, una bioplastica, superasse quel test e raggiungesse la classificazione V-0 completa è stata una vera sfida".
Le prestazioni aggiuntive di Dura-Tech e Therma-Tech comportano inevitabilmente alcuni compromessi sulla sostenibilità, dato che nessuno dei due prodotti è compostabile. Tuttavia, entrambi hanno potenziale per il riciclaggio chimico e meccanico.
"Il riciclaggio chimico del PLA sta diventando una vera realtà commerciale ora, quindi non dobbiamo ridurre il ciclo del materiale", ha affermato Gill. "Se si ricicla meccanicamente un qualsiasi polimero, probabilmente si comprometteranno alcune delle proprietà. Ma con il riciclaggio chimico, in realtà filtriamo solo il ritardante di fiamma e otteniamo la materia prima in modo da poter rigenerare il polimero vergine".
Ma i maggiori vantaggi si hanno a monte, con l'impronta dei prodotti Floreon che non deriva da carbonio fossile. A valle, ciò significa che anche se il materiale finisce incenerito, la CO2 rilasciata sarà stata catturata di recente come biomassa, il che significa che il suo impatto ambientale sarà molto inferiore a quello della plastica incenerita ricavata da idrocarburi.
Per la maggior parte, l'incenerimento sarà l'ultima spiaggia. Le plastiche durevoli di Floreon sono progettate per il lungo periodo e dovrebbero finire in flussi di riciclaggio appropriati a fine vita. Di conseguenza, la biodegradabilità è meno preoccupante, sacrificata a favore delle prestazioni.
Per i biopolimeri monouso, la biodegradabilità è essenziale. Smaltiti tramite riciclaggio, discarica o come rifiuti, devono essere in grado di decomporsi in composti innocui in un lasso di tempo ragionevole, senza alcun impatto negativo sull'ambiente.
quapak di Birmingham ha sviluppato un materiale che si dice faccia esattamente questo. Noto come Hydropol, il polimero brevettato è idrofilo, si dissolve in modo innocuo in acqua, una proprietà utile per una classe di materiali che spesso finisce nei sistemi idrici sia per caso che per scelta.
"Si basa su una materia prima chiamata alcol polivinilico (PVOH), che esiste da molto tempo, ma noi lo formuliamo in modo tale che sia possibile elaborarlo termicamente", ha detto a The Engineer Mark Lapping, CEO di Aquapak .
"È già utilizzato in cose come cuciture e dispositivi medici, pastiglie per lavastoviglie, quel genere di cose, ma nessuno lo ha reso tale da poterlo elaborare saldamente per l'imballaggio o per beni di consumo. Ecco qual è il nostro punto di differenza".
In modo simile a Xampla, l'obiettivo di Aquapak è la plastica monouso che può interrompere i flussi di riciclaggio a fine vita. Secondo Lapping, Hydropol può essere utilizzato per produrre cose come sacchetti per indumenti, pacchetti di patatine e bustine, articoli che troppo spesso finiscono come rifiuti e vengono lavati nei corsi d'acqua. Come Morro di Xampla, Hydropol può anche essere utilizzato come rivestimento barriera per cartone o carta. Il materiale si dissolve durante il riciclaggio, lasciando la polpa fibrosa incontaminata.
"Le plastiche tradizionali si attaccano alla carta e non si separano", ha spiegato Lapping. "Quindi, ciò crea un vero problema a valle per i riciclatori di carta, perché finiscono con questa poltiglia viscida con plastica e carta mescolate insieme.
"Il nostro materiale passa in soluzione, come lo zucchero nel tè, nell'impianto di depurazione, dove si biodegraderà completamente, sia in modo aerobico che anaerobico."
A differenza dei prodotti Xampla e Floreon, Hydropol è attualmente derivato da fonti petrolchimiche, il che significa che non è propriamente un biopolimero. Tuttavia, Aquapak sta esplorando materie prime PVOH di origine biologica per rafforzare ulteriormente le credenziali verdi del materiale.
Inoltre, a differenza di Xampla e Floreon, Aquapak mantiene tutta la produzione internamente, optando contro la strada delle licenze. La sua fabbrica di 30.000 piedi quadrati può produrre 10.000 tonnellate di pellet Hydropol all'anno, utilizzando la formulazione ed il processo brevettati di Aquapak. Il controllo sulla produzione è un importante punto di differenza per l'azienda, secondo Lapping.
"Ecco perché volevamo una nostra fabbrica per controllare questo, perché devi controllare la reazione nella composizione per poter realizzare il prodotto", ha detto. "Ci sono voluti 10 anni di R&S per riuscire a creare qualcosa di assolutamente unico".
A seconda dell'applicazione, Aquapak può produrre Hydropol con diversi gradi di solubilità, studiati per degradarsi in acqua a diverse temperature.
"Possiamo formulare qualsiasi cosa tra 25 e 80 gradi (C)", ha detto Lapping. "Ad esempio, il nostro prodotto viene utilizzato per realizzare borse per indumenti in Asia... quel materiale è formulato per dissolversi a temperature superiori a 70 gradi centigradi, quindi non si decomporrà in presenza di un po' di umidità nell'atmosfera".
Al contrario, i prodotti che difficilmente vengono esposti in ambienti con elevata umidità potrebbero dissolversi in acqua ad una temperatura di soli 25°C, simile alla temperatura riscontrata nella maggior parte delle piscine. Ma anche i prodotti progettati per resistere a temperature più elevate si decomporranno in presenza di acque più fredde, anche se per periodi di tempo più lunghi.
"Vuoi assicurarti che l'applicazione per cui la utilizzi durante il ciclo di vita si adatti alle condizioni in cui verrà utilizzata, ma alla fine del ciclo di vita vuoi sapere che si romperà in modo sicuro", ha affermato Lapping.
Nel 2024, Hydropol è stato utilizzato da The British Crisp Co. per creare quello che si dice essere il primo pacchetto di patatine completamente riciclabile al mondo. L'organizzazione non-profit OPRL per il riciclaggio ha certificato le confezioni per i flussi di raccolta a bordo strada, con i consumatori che le hanno incluse nel loro materiale cartaceo.
Con i britannici che consumano la sbalorditiva cifra di 8 miliardi di pacchetti di patatine ogni anno, praticamente tutti destinati a finire in discarica od all'incenerimento, questo ci ricorda sia la portata del problema della plastica sia la capacità dei nuovi materiali di avere un impatto. Nei prossimi anni, i polimeri monouso che non si biodegradano potrebbero persino diventare un ricordo del passato. Sono un sacco di pacchetti di patatine, scatole da asporto e tazze da caffè che devono essere sostituite. E un'enorme opportunità per le aziende che progettano le soluzioni.
ENGLISH
Advances in the development of biopolymers and alternative plastics could help address the mountains of plastic waste produced each year. Andrew Wade reports.
Plastics, much like the hydrocarbon cousins they’re derived from, are inherently useful. Cheap, abundant, and multifunctional, they touch virtually every aspect of daily life, from clothing, packaging and consumer goods to electronics, automotive components and medical devices.
But this utility has fuelled ubiquity and, in the absence of adequate circular practices, plastic waste has become a major environmental hazard. Around 450 million tonnes of plastic waste is generated globally each year, with less than 10 per cent recycled. The remainder is incinerated, sent to landfill or littered, with an estimated 2 million tonnes washing into our oceans.
At this stage the problem is well known but, just as with fossil fuels, behaviour has been resistant to change. In December 2024, representatives from nearly 200 countries came together for the INC-5 talks with the aim of establishing a global plastics treaty. However, just as with the COP talks to tackle emissions, major oil-producing countries blocked meaningful progress.
One of the main challenges with new materials like bioplastics in general, is that they do not easily integrate with existing recycling streams
Dr Marc Rodriguez Garcia, Xampla
In the absence of a global agreement, the best hope for tackling the plastics crisis may lie with technology - tweaking plastics to make them biodegradable or replacing petrochemical feedstocks with plant material. And with a global plastics market north of $700 billion - set to top $1 trillion by 2033 – the incentive is financial as much as it’s environmental.
One of the biggest challenges is single-use plastics, pervasive across everything from packaging and FMCG (fast moving consumer goods) to takeaway boxes and coffee cups. While many single-use items – plastic straws for example - can be easily identified and replaced with greener alternatives, others are less visible and have functionality that biomaterials struggle to match.
“I think one of the main challenges with new materials like bioplastics in general, is that they do not easily integrate with existing recycling streams,” Dr Marc Rodriguez Garcia, co-founder and CTO at Xampla, told The Engineer.
Spun out of Cambridge University, Xampla converts protein feedstocks from plants such as peas, potatoes and rapeseed into sustainable biopolymer materials. Initially aiming to replace a range of single-use plastics, more recently the company has narrowed its focus.
“Most of our progress has actually been on focusing on certain applications where, essentially, our materials can replace the types of plastics which are impossible to recycle,” said Rodriguez Garcia.
Plastics, much like the hydrocarbon cousins they’re derived from, are inherently useful. Cheap, abundant, and multifunctional, they touch virtually every aspect of daily life, from clothing, packaging and consumer goods to electronics, automotive components and medical devices.
But this utility has fuelled ubiquity and, in the absence of adequate circular practices, plastic waste has become a major environmental hazard. Around 450 million tonnes of plastic waste is generated globally each year, with less than 10 per cent recycled. The remainder is incinerated, sent to landfill or littered, with an estimated 2 million tonnes washing into our oceans.
At this stage the problem is well known but, just as with fossil fuels, behaviour has been resistant to change. In December 2024, representatives from nearly 200 countries came together for the INC-5 talks with the aim of establishing a global plastics treaty. However, just as with the COP talks to tackle emissions, major oil-producing countries blocked meaningful progress.
One of the main challenges with new materials like bioplastics in general, is that they do not easily integrate with existing recycling streams
Dr Marc Rodriguez Garcia, Xampla
In the absence of a global agreement, the best hope for tackling the plastics crisis may lie with technology - tweaking plastics to make them biodegradable or replacing petrochemical feedstocks with plant material. And with a global plastics market north of $700 billion - set to top $1 trillion by 2033 – the incentive is financial as much as it’s environmental.
One of the biggest challenges is single-use plastics, pervasive across everything from packaging and FMCG (fast moving consumer goods) to takeaway boxes and coffee cups. While many single-use items – plastic straws for example - can be easily identified and replaced with greener alternatives, others are less visible and have functionality that biomaterials struggle to match.
“I think one of the main challenges with new materials like bioplastics in general, is that they do not easily integrate with existing recycling streams,” Dr Marc Rodriguez Garcia, co-founder and CTO at Xampla, told The Engineer.
Spun out of Cambridge University, Xampla converts protein feedstocks from plants such as peas, potatoes and rapeseed into sustainable biopolymer materials. Initially aiming to replace a range of single-use plastics, more recently the company has narrowed its focus.
“Most of our progress has actually been on focusing on certain applications where, essentially, our materials can replace the types of plastics which are impossible to recycle,” said Rodriguez Garcia.
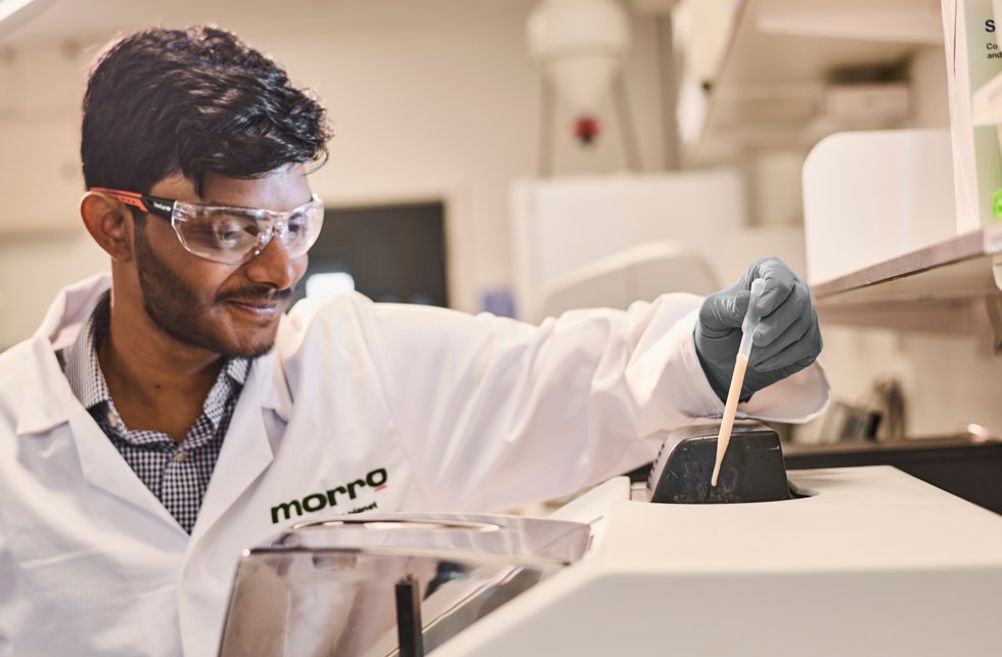
A primary target for Xampla are the thin plastic coatings applied to cardboard and paper that act as a barrier against grease or liquids. These super thin layers of polymers – sometimes containing PFAS or ‘forever chemicals’ – are prevalent in coffee cups and takeaway boxes. The coatings can be particularly pernicious as consumers often believe the packaging is recyclable, when in fact the plastic layers contaminate recycling streams.
“Coatings on paper, for example, these are the types of very thin layers of plastics that are too small to be captured in existing recycling waste streams, and especially if they’re part of a separate material like a cardboard box,” said Rodriguez Garcia.
“The paper potentially can be recycled, but a very thin plastic layer, which is only like a few microns thick…that’s very thin to actually be captured in the recycling stream…the highest likelihood for them is to end up being incinerated or actually leaking into the environment. So all of our applications are specifically focused on trying to replace those invisible plastics and I think that’s now become our USP.”
Xampla’s Morro coating provides similar functionality to these existing plastic coatings but allows the underlying paper or cardboard to be recycled. A deal last year with Finnish consumer packaging company Huhtamäki and the 2M Group of Companies will see takeaway boxes featuring Morro rolled out commercially. This follows a licensing agreement between Xampla and 2M for the latter to produce Morro at industrial scale.
“Manufacturing these materials at scale, it takes a lot of investment and it fundamentally takes a lot of expertise,” said Rodriguez Garcia. “That’s why we decided to go down the route of licensing and these partnerships with companies like 2M who have been manufacturing chemicals and other bio-based ingredients for decades.”
Another emerging use case for Xampla’s technology is microencapsulation – using the biopolymer to encase things like fragrance oils or vitamins in liquids. Often deployed in cosmetics or personal care products, microencapsulation protects ingredients and can extend shelf life but relies on harmful microplastics to do so. Xampla’s tech offers a biodegradable alternative.
“There’s like tens of thousands of tons of these intentionally added microplastics leaking directly into the environment,” said Rodriguez Garcia. “We can provide a completely natural polymer alternative to an existing plastic material that’s being used in that application.”
These single-use ‘invisible’ applications targeted by Xampla are relatively low hanging fruit where biopolymers could have a transformative effect. But it is not just the consumer segment that is driving change. The versatility of plastics means they play a role in almost every engineering sector, where durability is often paramount.
Floreon, another UK university spinout, specialises in high performance bioplastics. Based around research that originated at the University of Sheffield, the company takes plant-based biopolymer feedstocks and enhances them for a range of applications including toys and electronics.
“We take PLA (polylactic acid), which is a green polymer made from plants,” Dr Andrew Gill, Floreon’s technical director, told The Engineer.
“We make it possible to take it into durable applications, applications that are higher value and have a longer service life. We buy the PLA readymade from a supplier and our patent is about blending PLA in the right way with things that give it the properties of an engineering plastic.”
The PLA that Floreon relies on is largely derived from sugarcane and corn. This raises questions around the sustainability of bioplastics, with feedstocks potentially crowding out food supplies. But according to Gill, bioplastics have a negligible impact on land use.
“To make all the bioplastics in the world today, I think we require less than 1/25 of 1 per cent of global agricultural area,” he said. “So we’re not competing with food production.”
Floreon has developed three core PLA-based products. Bio-Tech is a food-safe, industrially compostable biopolymer and the greenest of the three. Stepping up from that is Dura-Tech, a tougher bioplastic with higher impact strength, which is recyclable but not compostable. Lastly comes Floreon’s latest development, Therma-Tech, a certified flame-retardant material to enable the use of bioplastics in a host of applications where they have previously been excluded.
“All of our grades have a lot of benefits in common,” said Gill. “They all have high renewable content. They have a low carbon footprint in production, and because of the low manufacturing temperatures, our customers can reduce their Scope Two emissions - the energy use in manufacturing - and their Scope Three emissions based on the carbon footprint of the materials in the products.”
Therma-Tech in particular has been garnering attention of late, helping Floreon scoop the Innovation Award at the Plastics Industry Association’s 2024 showpiece event. A first of its kind, the halogen-free flame-retardant biopolymer is opening doors for the company, taking bioplastics into applications that were previously off limits.
To make all the bioplastics in the world today we require less than 1/25 of 1 per cent of global agricultural area
Dr Andrew Gill - Floreon
“It’s a really standout innovation in that we’re not just competing with bioplastics, but we’re able to replace fire resistant engineering plastics such as flame-retardant ABS (acrylonitrile butadiene styrene),” said Gill. “Fire-retardant plastics - there’s a lot of concerns about the health and environmental impacts of the halogenated flame retardants that are being used today in those applications.”
Due to the potential for short circuits, plastics used in electronic devices must have a certain level of fire resistance. The specific classification Floreon’s customers were chasing was UL 94 V-0, an industry standard where a vertical sample of material is set alight from below, then must self-extinguish safely within 10 seconds with no flaming drips.
“When that stops, they put the flame back on again for a further 10 seconds and do the same,” Gill explained. “Getting a plant-based material, a bioplastic, to pass that test and achieve the full V-0 rating was a real challenge.”
The added performance of Dura-Tech and Therma-Tech inevitably comes with some trade-offs on sustainability, with neither product being compostable. However, both have potential for chemical as well as mechanical recycling.
“Chemical recycling of PLA is becoming a real commercial reality now, so we don’t have to downcycle the material,” said Gill. “If you mechanically recycle any polymer, you’re probably going to compromise some of the properties. But with chemical recycling, we actually just filter out the flame retardant and we get the feedstock back so we can regenerate virgin polymer.”
But the biggest benefits originate upstream, with the footprint of Floreon’s products not deriving from fossil carbon. Downstream, this means that even if the material does end up incinerated, the CO2 released will have been recently captured as biomass, meaning its environmental impact will be much less than incinerated plastic made from hydrocarbons.
For the most part, incineration will be a last resort. Floreon’s durable plastics are designed for the long haul and should end up in appropriate recycling streams at end-of-life. As a result, biodegradability is less of a worry, sacrificed in favour of performance.
For single-use biopolymers, biodegradability is essential. Disposed of in recycling, landfill or as litter, they need to be able to break down into harmless compounds over a reasonable timeframe, with no adverse impact on the environment.
rmingham’s Aquapak has developed a material claimed to do exactly that. Known as Hydropol, the patented polymer is hydrophilic, dissolving harmlessly in water – a handy property for a class of material that frequently ends up in water systems by both accident and design.
“It’s based on a raw material called polyvinyl alcohol (PVOH), which has been around a long time, but we formulate it in such a way that you can thermally process it,” Mark Lapping, Aquapak’s CEO, told The Engineer.
“It’s already used in things like stitching and medical devices, dishwasher tablets, that type of thing, but no one made it so they could firmly process it for packaging or for consumer goods. That’s what our point of difference is.”
In a similar vein to Xampla, Aquapak’s target is the single-use plastic that can disrupt recycling streams at end-of-life. According to Lapping, Hydropol can be used to manufacture things like garment bags, crisp packets and sachets, items that too often end up as litter and washed into watercourses. Like Xampla’s Morro, Hydropol can also be used as a barrier coating for cardboard or paper. The material dissolves during recycling, leaving the fibrous pulp uncontaminated.
“Traditional plastics will stick to paper and don’t separate,” Lapping explained. “So it gives a real problem downstream for the paper recyclers, because they end up with this gooey mush with plastic and paper mixed together.
“Our material passes in solution, like sugar in your tea, into the effluent plant, where we’ll fully biodegrade, both aerobically and anaerobically.”
Unlike Xampla and Floreon’s products, Hydropol is currently derived from petrochemical sources, meaning it is not strictly a biopolymer. However, Aquapak is exploring bio-based PVOH feedstocks to further bolster the material’s green credentials.
Also in contrast to Xampla and Floreon, Aquapak keeps all manufacturing in-house, opting against the licensing route. Its 30,000 square foot factory can produce 10,000 tonnes of Hydropol pellets annually, using Aquapak’s patented formulation and process. Control over production is an important point of difference for the company, according to Lapping.
“That’s why we wanted our own factory to control that, because you have to control the reaction in the compounding to be able to make the product,” he said. “It’s been 10 years of R&D to be able to create something that is absolutely unique.”
Depending on the application, Aquapak can manufacture Hydropol with various degrees of solubility, designed to degrade in water of different temperatures.
“We can formulate everything between 25 degrees and 80 degrees (C),” said Lapping. “For instance, our product goes into making garment bags in Asia…that material is formulated to dissolve above 70 degrees centigrade, so it’s not going to break down in the presence of a bit of humidity in the atmosphere.”
Conversely, products unlikely to see exposure in high moisture environments could dissolve in water as low as 25°C, similar to the temperature found in most swimming pools. But even the products designed to withstand higher temperatures will break down in the presence of cooler waters, albeit over longer periods of time.
“You want to make sure the application you’re using it for in life fits the conditions that it’s going to be used in, but at the end of life, you want to know it’s going to break down safely,” said Lapping.
In 2024, Hydropol was used by The British Crisp Co. to create what’s claimed to be the world’s first fully recyclable crisp packet. Recycling non-profit OPRL certified the packs for kerbside collection streams, with consumers including it with their paper material.
With Brits getting through an astounding 8 billion packets of crisps each year – virtually all ending up in landfill or incineration - it’s a reminder of both the scale of the plastics problem and the capacity for new materials to make an impact. In the coming years, single-use polymers that don’t biodegrade may even become a thing of the past. That’s a lot of crisp packets, takeaway boxes and coffee cups that need replacing. And a huge opportunity for the companies engineering the solutions.
Da:
https://www.theengineer.co.uk/content/in-depth/how-advances-in-alternative-plastics-could-help-address-the-waste-crisis
Commenti
Posta un commento