Vital capacity – the story behind Penlon’s ventilator push / Capacità vitale: la storia dietro la spinta del ventilatore di Penlon
Vital capacity – the story behind Penlon’s ventilator push / Capacità vitale: la storia dietro la spinta del ventilatore di Penlon
Segnalato dal Dott. Giuseppe Cotellessa / Reported by Dr. Giuseppe Cotellessa
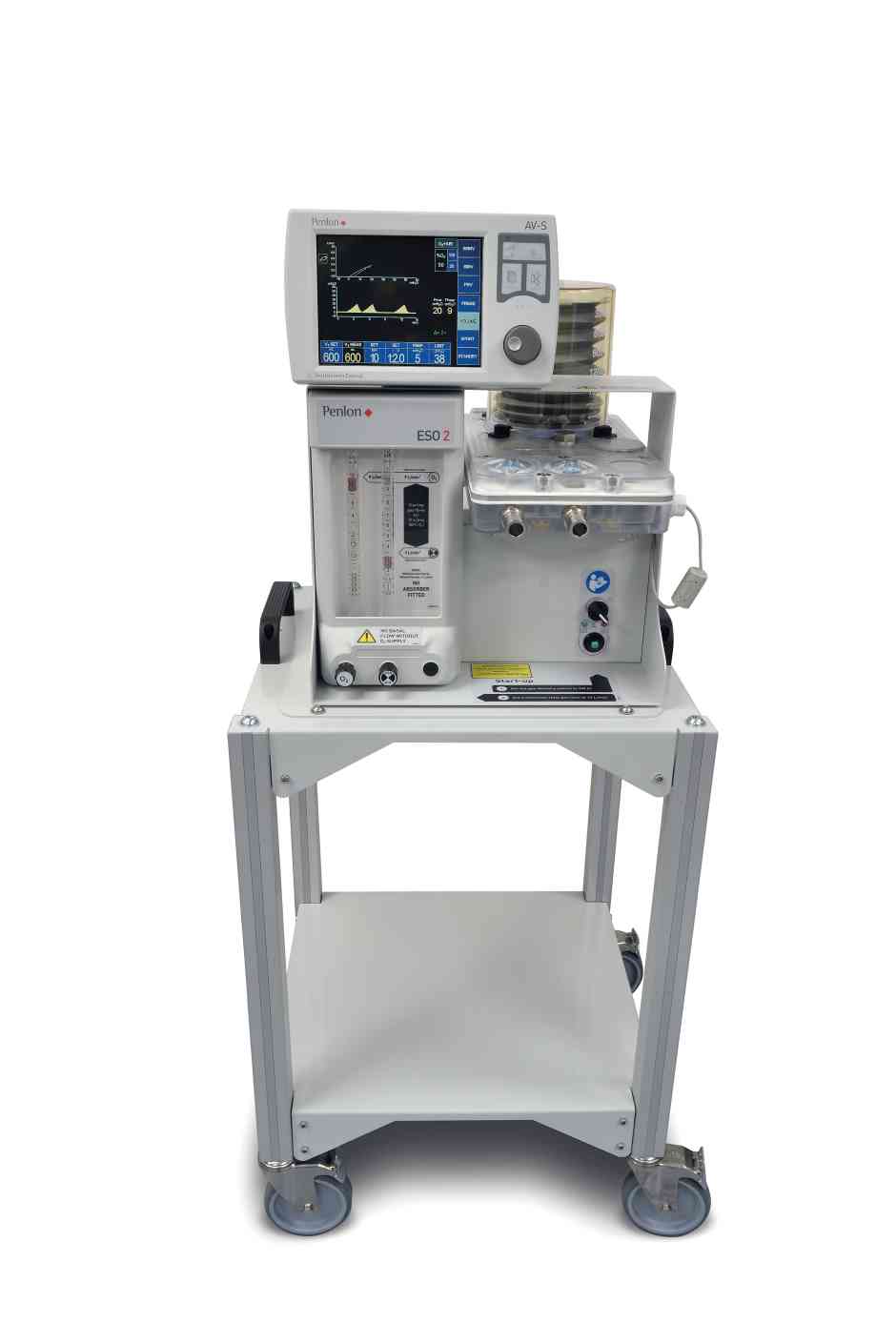
Penlon’s ESO2 ventilator. / Ventilatore ESO2 di Penlon. Image: Andrew Garnham, Penlon Ltd
Whilst the UK’s push for extra Covid-19 ventilators pulled in some of the biggest names in manufacturing, it was the expertise of little-known Oxfordshire medical devices firm – Penlon – that was to prove critical to the project’s success. Jon Excell spoke to the company’s production engineering manager Paul Merrick about what it was like to be thrust into the heart of a national effort.
Engineers love a challenge. And there are few more striking examples of this appetite in action than the events of April 2020, when teams from almost every corner of the UK’s engineering landscape dropped what they were doing to rapidly work up concepts and designs for urgently needed ventilators.
The offers of help from across the manufacturing spectrum were a humbling reminder of both the importance of engineers at a time of crisis and the UK’s rich pool of engineering talent. But – as previously reported by The Engineer – the push for ventilators quickly coalesced around Ventilator Challenge UK, a consortium of manufacturers which took the sensible decision not to reinvent the wheel, but to scale-up the production of two existing devices: a portable ventilator manufactured by Luton’s Smiths Group and the Prima ESO2, a ventilator design adapted from anaesthesia equipment produced by Oxfordshire medical devices firm Penlon.
Earlier this summer, The Engineer caught up with Penlon’s production engineering manager Paul Merrick, who provided a fascinating glimpse of that intense, nerve-shredding few months when the small firm found itself at the heart of UK manufacturing’s celebrated Covid-19 response.
“I’ve never experienced anything like it before,” said Merrick. “We went from what we’d make in a year [600 units] to making that in two days and ramping it up over seven weeks – it’s incredible what was done to achieve it.”
As one of a handful of UK ventilator manufacturers, Penlon was quick out of the blocks responding to the crisis; immediately ramping up production of its core product – a specialised anesthesia ventilator – at its Oxfordshire site and concentrating on the domestic market. But as a relatively small manufacturer it knew that without a rethink and significant amounts of help it wouldn’t be able to make much of a dent in the huge projected demands. So, when the government call went out for a Rapidly Manufactured Ventilator System (RMVS) it joined forces with the Ventilator Challenge UK Consortium to explore how its device could be adapted for mass manufacture.
This process was primarily about simplifying the design and modifying the system to run for extended periods of time, explained Merrick. “We had to cut some of the complexity out to make it simpler. For instance, normally you’d have a CO2 absorption unit because you don’t want to throw away your expensive anesthetic agent – it goes round and round in a closed circle loop. But that wasn’t required here, we made it much simpler so it’s just constantly feeding through the gas rather than recircling it.”
Other key modifications – such as the removal of a full anesthesia carts – were focused on making the system to easier to transport and manufacture.
At this point, with the design in place, and a handful of new devices assembled and validated at Penlon’s facility, the consortium sprang into action. And the impact of this sudden injection of intellectual horsepower and technical resources was, said Merrick, electric. “On a Friday in late March we were introduced to the consortium, on the Saturday they were in all day; on Sunday I had teams in learning how to build ventilators, and after that it never stopped.”
Penlon’s manufacturing and assembly was then effectively outsourced to scaled up parallel production facilities across the consortium. Ford began making the ventilators; Airbus set up a production line to produce flow meter machines; McLaren pivoted from Formula 1 to medical device trolleys, and specialist electronics manufacturer STI concentrated on the assembly. Critically – in order to ensure that the end product met the carefully regulated standards required for medical devices – all of these companies became an extension of Penlon, working from its instructions and under its quality systems. Final test of all systems was carried out at Penlon HQ.
The resource suddenly available to the Penlon team was, said Merrick, an inspiring illustration of the “can-do” spirit of UK manufacturing. “The word “can’t” doesn’t exist,” he said. “It’s “how can we?” everyone pushes themselves as fast as they can to get it done.” He added that working with the consortium partners, some of whom were more accustomed to satisfying the time-sensitive demands of Formula 1, was a real eye-opener for a firm more used to the relatively measured pace of the medical technology world. “During normal time, one week is the equivalent to one hour at Penlon. Whatever you do in week, you’ve got to do it in an hour. That’s the intensity”.
The achievements of the consortium are now well known: 13,000 devices were delivered the NHS, and whilst – thankfully – many of them haven’t yet been required, the UK is now well equipped should the need arise in the future.
To get to this point in just three months was an astonishing achievement. But, said Merrick, it wasn’t without its challenges.
One major issue, he said, was ramping up the supply chain alongside the manufacturing operation. Many existing suppliers simply didn’t have the capacity to meet this sudden increase in demand, so finding new suppliers, and quickly getting them up to speed on what was required was tricky.
But from Merrick’s point of view, perhaps the biggest issue, was finding ways of rapidly sharing the expert knowledge of Penlon’s small group of engineers across the consortium. “We’re quite a small team here at Penlon and all the knowledge is here so we’re trying to disseminate all of the information across the consortium and there are a few people here who are key to it. There’s nowhere to hide!”
Protecting these “knowledge holders”, and ensuring that they weren’t burnt out by the 24-7 demands of the project was a key priority, and the team was carefully structured to ensure that this critical team of engineers had plenty of support from other member of the consortium. Merrick, for instance, had two McLaren engineers working alongside him throughout.
Technology also played a role here, with Microsoft’s mixed-reality HoloLens technology widely used to enable engineers across the consortium to collaborate and share knowledge remotely. “The Ford engineer would be on the machine and our engineer at Penlon would be talking him through the issues and working with him and saying “you need to change that, you need to do this,” said Merrick. “To be with them directly while they’re working -and see exactly what they’re seeing and be able to talk to them straight away – made a big difference.”
With the urgent government-led push for ventilators officially stood down the team is now able to return to a less frenetic pace of working, and its key staff can start enjoying some well-deserved relaxing weekends.
Nevertheless, Merrick said that there are a number of lessons learned from the experience that will stay with the company for a long time.
Most obviously, the group now has experience of what it takes to rapidly scale up manufacture, and it’s now looking at how these lessons could potentially be applied to the production of a mass market device for export around the world.
Whilst much of this is about the application of technology and processes, none of it would be possible without the people, and Merrick said perhaps the biggest lesson he learned was the strength and versatility of the people around him. “I’ve learned how people react to these sorts of things and how they perform under pressure,” he said. “You don’t really know a person until you’ve worked through one of these situations…that was something that I know the team around me are immensely strong.”
More generally, he feels that the work of the consortium should serve as a reminder of the critical role played by engineers in our society. “We do generally overlook what our engineers do for us and we don’t always respect the name of engineers like other countries do – but without the engineers who made all this happen, put these lines together, put these process plans together, it just wouldn’t have happened. I don’t think there’s a day goes by when we don’t use engineers for something.”
ITALIANO
Mentre la spinta del Regno Unito per i ventilatori Covid-19 extra ha attirato alcuni dei più grandi nomi nella produzione, è stata la competenza della nota azienda di dispositivi medici dell'Oxfordshire - Penlon - che si è rivelata fondamentale per il successo del progetto. Jon Excell ha parlato con Paul Merrick, responsabile dell'ingegneria della produzione, di come è stato essere spinti nel cuore di uno sforzo nazionale.
Gli ingegneri amano una sfida. E ci sono alcuni esempi più sorprendenti di questo appetito in azione rispetto agli eventi dell'aprile 2020, quando i gruppi di quasi ogni angolo del panorama ingegneristico del Regno Unito hanno abbandonato ciò che stavano facendo per elaborare rapidamente concetti e progetti per i ventilatori urgentemente necessari.
Le offerte di aiuto in tutto lo spettro della produzione sono state un umiliante promemoria dell'importanza degli ingegneri in un momento di crisi e del ricco pool di talenti ingegneristici del Regno Unito. Ma - come precedentemente riportato da The Engineer - la spinta per i ventilatori si è rapidamente consolidata attorno a Ventilator Challenge UK, un consorzio di produttori che ha preso la ragionevole decisione non di reinventare la ruota, ma di aumentare la produzione di due dispositivi esistenti: un ventilatore portatile prodotto da Luton's Smiths Group e Prima ESO2, un progetto del ventilatore adattato da apparecchiature per anestesia prodotte dalla ditta di dispositivi medici Oxfordshire Penlon.
All'inizio di questa estate, The Engineer ha incontrato Paul Merrick, responsabile dell'ingegneria di produzione di Penlon, che ha dato uno sguardo affascinante a quei mesi intensi e devastanti, quando la piccola azienda si è trovata al centro della celebre risposta Covid-19 della manifattura britannica.
"Non ho mai provato nulla di simile prima", ha dichiarato Merrick. "Siamo passati da quello che avremmo fatto in un anno [600 unità] a farlo in due giorni e accelerarlo in sette settimane - è incredibile quello che è stato fatto per raggiungerlo."
Come uno dei pochi produttori britannici di ventilatori, Penlon è uscito rapidamente dai blocchi per rispondere alla crisi; accelerare immediatamente la produzione del suo prodotto principale - un ventilatore specializzato per anestesia - nel suo sito nell'Oxfordshire e concentrarsi sul mercato interno. Ma come produttore relativamente piccolo sapeva che senza un ripensamento e una quantità significativa di aiuto non sarebbe stato in grado di fare molta strada nelle enormi richieste previste. Quindi, quando la richiesta del governo è uscita per un sistema di ventilazione rapido (RMVS), ha unito le forze con il Consorzio Ventilator Challenge UK per esplorare come il suo dispositivo potesse essere adattato per la produzione di massa.
Questo processo riguardava principalmente la semplificazione della progettazione e la modifica del sistema per l'esecuzione per lunghi periodi di tempo, ha spiegato Merrick. “Abbiamo dovuto ridurre un po' della complessità per renderla più semplice. Ad esempio, normalmente avresti un'unità di assorbimento di CO2 perché non vuoi buttare via il tuo costoso agente anestetico: gira e rigira in un circuito chiuso. Ma questo non era necessario qui, lo abbiamo reso molto più semplice, quindi si è proceduto solo costantemente alimentando il gas piuttosto che metterlo in ricircolo. "
Altre modifiche chiave - come la rimozione di carrelli per anestesia completa - sono state incentrate sulla semplificazione del trasporto e della fabbricazione del sistema.
A questo punto, con la progettazione in atto e una manciata di nuovi dispositivi assemblati e validati nella struttura di Penlon, il consorzio è entrato in azione. E l'impatto di questa improvvisa iniezione di potenza intellettuale e risorse tecniche fu, disse Merrick, elettrico. “Un venerdì di fine marzo ci è stato presentato il consorzio, il sabato sono rimasti tutto il giorno; domenica ho avuto dei gruppi per imparare a costruire i ventilatori, e dopo di ciò non si è mai fermato ”.
La produzione e l'assemblaggio di Penlon sono stati quindi esternalizzati in modo efficace per ampliare le strutture di produzione parallele in tutto il consorzio. Ford iniziò a fabbricare i ventilatori; Airbus ha istituito una linea di produzione per la produzione di macchine per misuratori di portata; La McLaren passò dalla Formula 1 ai carrelli per dispositivi medici e il produttore specializzato di elettronica STI si concentrò sull'assemblaggio. Criticamente - al fine di garantire che il prodotto finale soddisfacesse gli standard attentamente regolamentati richiesti per i dispositivi medici - tutte queste società sono diventate un'estensione di Penlon, lavorando sulle sue istruzioni e secondo i suoi sistemi di qualità. Il test finale di tutti i sistemi è stato effettuato presso il quartier generale di Penlon.
La risorsa improvvisamente disponibile per il gruppo di Penlon è stata, ha dichiarato Merrick, un'illustrazione ispiratrice dello spirito "can-do" della produzione britannica. "La parola" non può "non esiste", ha detto. "È" come possiamo? " tutti si spingono il più velocemente possibile per farlo." Ha aggiunto che lavorare con i partner del consorzio, alcuni dei quali erano più abituati a soddisfare le esigenze sensibili al tempo della Formula 1, è stato un vero toccasana per un'azienda più abituata al ritmo relativamente misurato del mondo della tecnologia medica. “Durante il normale orario, una settimana equivale a un'ora a Penlon. Qualunque cosa tu faccia in settimana, devi farlo in un'ora. Questa è l'intensità ".
I risultati del consorzio sono ormai ben noti: 13.000 dispositivi sono stati consegnati al SSN e, per fortuna, molti di essi non sono ancora stati richiesti, il Regno Unito è ora ben attrezzato in caso di necessità in futuro.
Arrivare a questo punto in soli tre mesi è stato un risultato sorprendente. Ma, ha detto Merrick, non è stato senza le sue sfide.
Un problema importante, ha affermato, è stato quello di accelerare la catena di approvvigionamento a fianco dell'operazione di produzione. Molti fornitori esistenti semplicemente non avevano la capacità di soddisfare questo improvviso aumento della domanda, quindi trovare nuovi fornitori e farli rapidamente al passo con le esigenze era difficile.
Ma dal punto di vista di Merrick, forse il problema più grande, era trovare modi per condividere rapidamente le conoscenze degli esperti del piccolo gruppo di ingegneri di Penlon in tutto il consorzio. "Siamo una squadra piuttosto piccola qui a Penlon e tutta la conoscenza è qui, quindi stiamo cercando di diffondere tutte le informazioni in tutto il consorzio e ci sono alcune persone qui che sono fondamentali. Non c'è nessun posto dove nascondersi! "
Proteggere questi "detentori della conoscenza" e garantire che non fossero esauriti dalle richieste 24-7 del progetto era una priorità fondamentale, e il gruppo è stato attentamente strutturato per garantire che questo gruppo critico di ingegneri avesse un ampio supporto da parte di altri membri del consorzio. Merrick, ad esempio, aveva due ingegneri della McLaren al fianco di lui.
Anche la tecnologia ha giocato un ruolo qui, con la tecnologia HoloLens di realtà mista di Microsoft ampiamente utilizzata per consentire agli ingegneri di tutto il consorzio di collaborare e condividere le conoscenze in remoto. "L'ingegnere Ford sarebbe sulla macchina e il nostro ingegnere di Penlon avrebbe parlato con lui dei problemi e lavorato con lui e dicendo" devi cambiarlo, devi farlo ", ha detto Merrick. "Stare con loro direttamente mentre stanno lavorando - e vedere esattamente quello che stanno vedendo ed essere in grado di parlare con loro subito - ha fatto una grande differenza".
Con la spinta urgente guidata dal governo per i ventilatori ufficialmente pronti, il gruppo è ora in grado di tornare a un ritmo di lavoro meno frenetico e il suo staff chiave può iniziare a godersi dei meritati weekend rilassanti.
Tuttavia, Merrick ha affermato che dall'esperienza ci sono un certo numero di lezioni apprese che rimarranno a lungo in compagnia.
Ovviamente, il gruppo ora ha esperienza di ciò che serve per aumentare rapidamente la produzione e sta ora esaminando come queste lezioni potrebbero essere potenzialmente applicate alla produzione di un dispositivo del mercato di massa per l'esportazione in tutto il mondo.
Mentre gran parte di questo riguarda l'applicazione della tecnologia e dei processi, nessuno di questi sarebbe possibile senza le persone, e Merrick ha detto che forse la lezione più grande che ha imparato era la forza e la versatilità delle persone che lo circondavano. "Ho imparato come le persone reagiscono a questo genere di cose e come si comportano sotto pressione", ha detto. "Non conosci davvero una persona fino a quando non hai affrontato una di queste situazioni ... era qualcosa che so che la squadra intorno a me è immensamente forte."
Più in generale, ritiene che il lavoro del consorzio dovrebbe servire da promemoria del ruolo critico svolto dagli ingegneri nella nostra società. "In genere trascuriamo ciò che i nostri ingegneri fanno per noi e non rispettiamo sempre il nome di ingegneri come fanno altri paesi - ma senza gli ingegneri che hanno fatto accadere tutto ciò, uniscono queste linee, uniscono questi piani di processo, semplicemente non sarebbe successo. Non penso che passi un giorno in cui non usiamo gli ingegneri per qualcosa ".
Da:
Commenti
Posta un commento